CT-100
STRONG ACID STYRENE
CATION EXCHANGE RESIN
BSR CT-100 is a premium grade, high capacity, sulfonated, polystyrene cation resin supplied in the sodium or hydrogen form as moist, tough, uniform, spherical beads. Ion exchange is the unit operation that allows the separation of dissolved ionic species through their transfer from the liquid phase to a solid exchanger material, where they replace other ions of the same electric sign that, in turn, pass to the liquid phase. In this reversible process, chemical transformations do not take place in the ionic species involved or in the exchanger material, enabling their recovery after the ion exchange. The interest for the applications of the ion exchange lies precisely in the possibility of reusing the exchanger material again and again. In order to do so, the material must previously undergo a regeneration process before recovering its initial conditions.
Most applications of ion exchange aim at removing a particular ionic species from a liquid solution, resulting in their specific separation and concentration in the solid phase. Industrial applications for ion exchange processes are numerous: recovery of metal cations in solution, separation of ion mixtures, purification of liquids, controlled release of a chemical species, salts recovery, etc.
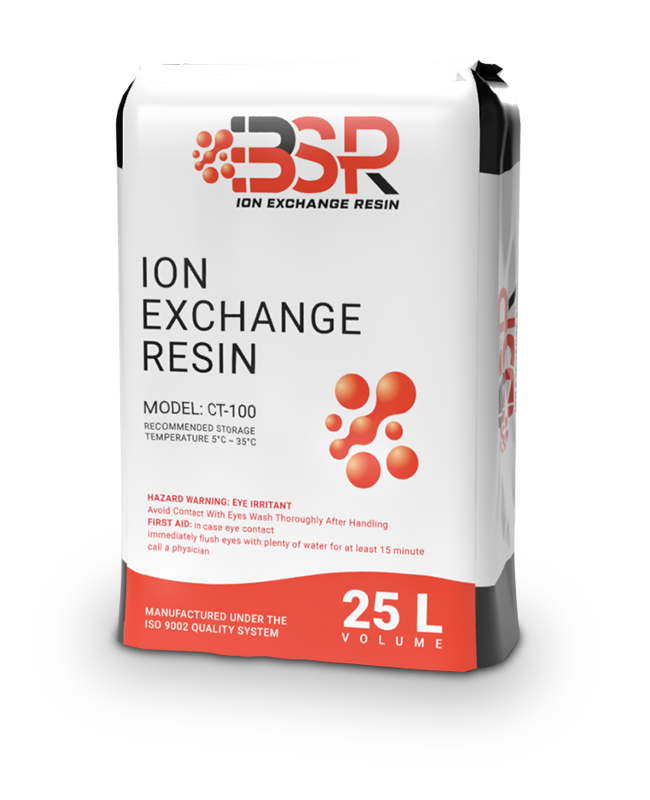
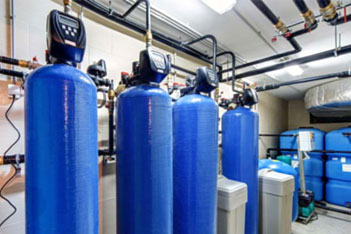
Water softening

Water demineralization
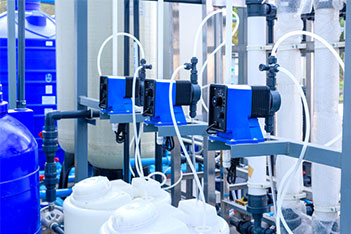
Alkalinity removal
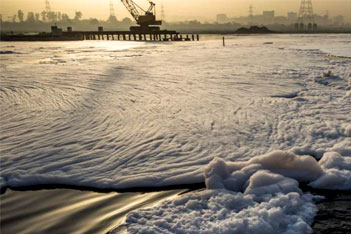
Removal of heavy metal cations dissolved in process water
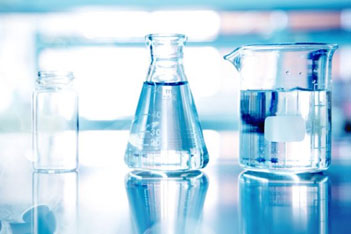
Removal of anions from strong acids, such as nitrate (NO3 - ) and sulfate (SO4 =)
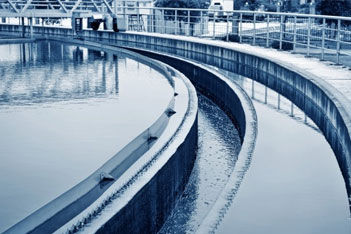
Ammonia removal at low temperatures.
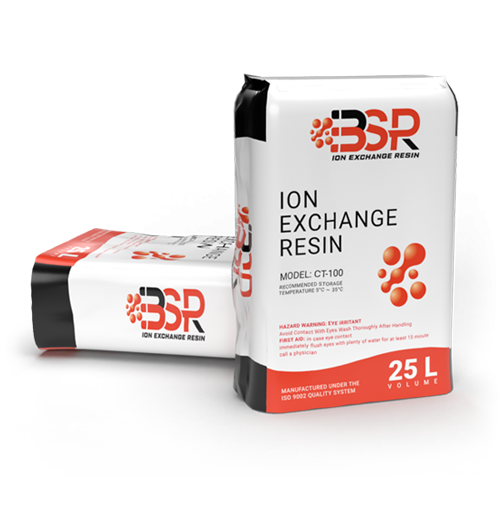
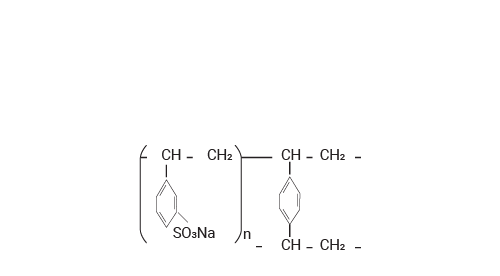
Also, inclusion of ion exchange as wastewater treatment and purification stage allows for removal (and eventual recovery) of ionic components in an effluent prior to final discharge or reuse, ensuring the required water quality in both cases. In addition to inorganic anions and metallic cations, many ionized organic molecules are also susceptible of being removed through ion exchange, including water-soluble dyes, resistant to conventional purification treatments and responsible for the color in the dyeing process effluents. Although various natural materials with exchange capacity are known, such as humus, clays and zeolites, synthetic exchange resins are normally used in ion exchange industrial practice, due to their operational advantages. Synthetic exchange resins are specifically designed for ion recovery under specific working conditions (aqueous medium, temperature, pressure, pH…). Ion exchange resins are typically presented in the form of spherical particles consisting of a cross-linked polymer in which specific functional groups are brought depending on the pursued application. Functional groups determine the nature of the ionic species exchanged between the resin and the aqueous
solution.
Application standard
- PH :1-14
- Max operation temperature: hydrogen type ≤100°C sodium type ≤120°C
- Shaping dilatability%: (H+-Na+)8-10
- Concentration of actified solution: NaCl:3-10%; HCl:4-5%; NaOH:4-5%
- Dosage of actified solution:
- NaCl:(8-10%); volume:resin volume =1.5-2:1
- HC1(4-5%) volume:resin volume =2-3:1
- NaOH(4-5%); volume:resin volume =2-3:1
- Flow of actified solution: 5-8m/h
- Regeneration contact time: 30-60min
- Conventional well-flushing flow: 10-20m/h
- Conventional well-flushing time: 30min
- Operational flow: 10-40m/h
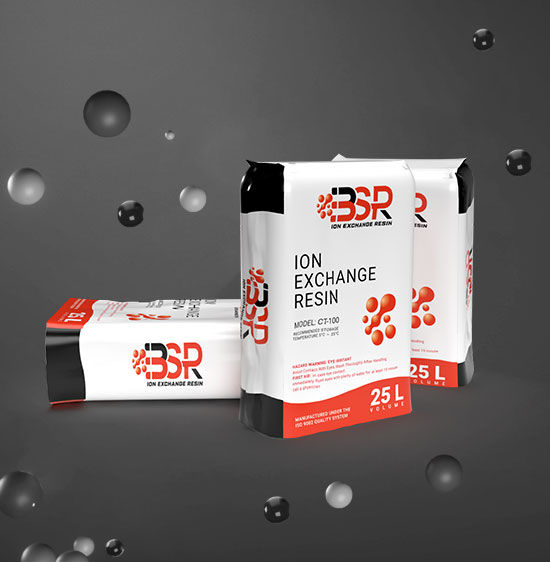
Ion exchange processes
An ion exchange system consists of a solid phase, insoluble (the ion exchanger material), surrounded by a liquid phase containing the solute of interest to be separated. Ion exchange process is established when the solid phase incorporates this solute to its structure without causing a permanent change. Ion exchange is always set between ionic species chemical equivalents of the same electric sign. The solid phase may be a crystalline lattice or a gel. If the exchanged ions are positive, the exchange material is called cationic, and anionic if the ionic species have a negative charge. Cations, such as calcium, magnesium, barium, strontium and radium, can be separated from an aqueous solution by using a cation-exchange resin. Similarly, anions like fluoride, nitrate, arsenate, selenate, chromate, as well as humic and fulvic acids can be separated by means of an anion-exchange resin. Synthetic resins are the most widely applied ion exchange materials for water treatment. These are durable materials, whose structural and functional groups are designed according to the specific applications to be obtained through the ion exchange. In order to optimize the bed mechanical and hydraulic properties, they are usually presented in the form of sphere. Ion exchange resins are produced from a polymer cross-linked structure, either polystyrene or acrylic polymer, which serves as structural material. Certain ionizable functional groups are incorporated to the basic polymer structure; that is, with acid or base characteristics. In aqueous solution and depending on their selectivity towards the ions contained in the solution, resin functional groups carry out the exchange process by replacing their counterions with the ions of interest to be removed from the solution. The exchange process between the resin and the aqueous solution comprises phases of diffusion, adsorption, electrostatic attraction and acid-base balance. The process is entirely reversible and under the appropriate acid or base conditions, the equilibrium can be moved in an anti-clockwise direction, resulting in the original chemical form of the resin (acidic, basic, salt). This property allows ion exchange resins to be used through many load and regeneration cycles. The cost effectiveness of treatment processes based on ion exchange is due precisely to the number of regeneration cycles that can be obtained with a specific resin under certain operating conditions and constitutes a major design factor
Operation cycle of an ion exchanger
Ion exchange applications at industrial scale proceed in cyclical operation processes until the exhaustion of the resin exchange capacity. Then, the subsequent regeneration of the resin is conducted. In practice, the technical and economic performance of an ion exchange process depends on the resin exchange capacity, the regenerant amount required in each operation cycle and the duty cycle length.
A typical duty cycle entails the following phases or stages
- Bed backwash through a clean water upflow, in order to remove possible particle remnants that accumulate on the resin bed during the operation phase, as well as the reclassification of the bed material, avoiding the formation of preferential channels.
- Resin regeneration: as the operation phase takes place, the exchange capacity of resins is reduced. Recovering of their optimal operating conditions is achieved by using regenerating solutions that restore their original ionic form, removing the ionic species of interest from the resin structure.
- Rinsing: upon the regeneration phase, it is appropriate to remove excess regenerating solution that may remain in the resin particle pores and bed interstices. Typically, a slow rinsing is carried out at low speed after the use of each regenerating solution, followed by a fast rinsing in order to remove any residual solution.
- Operation: the water to be treated is circulated through the bed, and collected at the exit together with the changed ionic composition. The ionic species of interest is integrated in the solid phase
Backwashings and bed expansion
Exchange resin beds regularly undergo a backwashing in order to remove the accumulated particles in the gaps and reclassify resin spheres in the bed by shaking them. The column backwashing should be carried out in such a way as to guarantee the optimal hydraulic performance of the bed during the operation and regeneration cycles. The backwashing is done by ascending an uniform water flow in the column, so that enough fluidization occurs in the bed to separate particles and fines accumulated during the production cycles. A typical water volume for backwashing would be equivalent to two complete displacements of the column freeboard. The resin bed should be expanded along the column, up to a height close to the backwashing water outlet collector in the column upper side. The ion exchange resin expansion depends on the resin sphere size, their density and the backwashing water temperature, so this is a characteristic value for each commercial resin.
The expansion percentage of an ion exchange column can be calculated according to the following formula:
% Bed expansion = 100 x (Fluidized bed height/Resting bed height)
Pressure Drop
The graph above shows the expected pressure loss per foot of bed depth as a function of flow rate at various Temperatures.
Backwash
After each cycle the resin bed should be backwashed at a rate that expands. The bed 50 to 75 percent. That will remove any foreign matter and reclassify the bed. The Graph above shows the expansion characteristics of BSR CT-100 in the sodium form.
Standard: GB13659-92
There are -SO3H groups on styrene -= ethene benzene polymer, its acidity is similar to HCl and H2SO4. It offer ion exchange capacity in basic, acid and neutral condition. It offer large exchange quantity, fast speed and good mechanical strength. Similar to USA :Amberlite IR-120, Dowex-50; Germany :Lewatit-100; France: Purolite C100-E
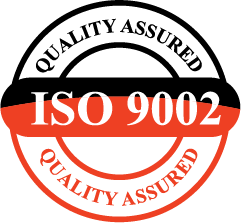
Storage and Handling of
Ion Exchange Resins
Storage of New, Unused Resin Standard demineralizing and softening resins experience minimal change in chemical properties over a 3 year shelf life. Resins should be stored in their original, unopened packaging in a cool, dry area. An indoor storage facility with climate control between 32–90°F (0–30°C) should be used for the best results. Storage temperatures above 90°F (30°C) can cause premature loss of capacity for anion resins, particularly those stored in the hydroxide form. Although cation resins can withstand higher temperatures, up to 120°F (50°C), it is best to store all resins under similar conditions. Storage temperatures below 32°F (0°C) can cause resin freezing, and temperatures below 0°F (–18°C) should be avoided. Tests of BSR resins under repeated freeze-thaw cycles show that bead damage can occur, so frozen resin must be thawed before safe loading can take place. Frozen resin should be thawed out completely under room-temperature conditions before loading and use.
Safety Aspects on Handling:
Ion exchange resins are generally not classified as hazardous materials, although resins in the hydrogen or hydroxide form are irritating to the eyes. A certain amount of attention should be paid during storage, handling, and processing of the resins. When sampling and installing, resin can emerge with considerable force in some cases. Care should also be taken to clean up spills of ion exchange resins because the small beads are very slippery when stepped on.
Loading/Unloading Resins:
Loading and unloading ion exchange resins from vessels can be done in a variety of ways, depending on the equipment design and procedures developed at the site. One simple means of transferring resin is through the use of eduction systems.
Preliminary Inspection before loading:
- Before loading the resins, make a detailed inspection of the empty vessel.
- Remove all debris of previous resins or foreign material.
- Clean up distributors and inspect all laterals, splash-plates, and nozzles for damage or plugging.
- Inspect the rubber lining, if present, for integrity, and perform a spark test, if possible.
- Whenever possible, check the pressure loss of the empty vessel at nominal flow rate and observe the flow patterns for uniformity.
CLEANING PROCEDURES:
Removal of Iron and Manganese from Cation Resins; Iron has a complex chemistry and may be present as inorganic precipitates (oxides/hydroxides), as cationic species, or as organometallic complexes. In water-treatment applications, iron is generally converted to the less-soluble Fe (III) form within the resin bed. Manganese also may be present as inorganic precipitates. The cleaning procedures is Air brushing system. This is used in condensate polishing and other water-treatment applications such as makeup demineralization to remove insoluble, particulate iron (crud).
The procedure are:-
- Exhaust the resin.
- Air-brush the bed and then backwash for 30 min.
- Regenerate the resin as normal.
If the particulates are large, backwashing may not be effective in removing them. In this case, the solids can be driven down to the bottom of the bed and removed through the screen/drain using the following procedure:
- Air-brush the bed for 30 s at a rate of approximately four volumes air per min per volume resin and then drain the bed for 30 s, adding more water at the top.
- Repeat step 1 about 10–20 times.
- Regenerate the resin as normal.
If soluble iron is also present, air-brushing should be followed by acid treatment.